Objective
Doosan Power Systems provides world-class cleaner, greener technology, products and services for power generation across the globe. As part of its strategy, Doosan needed to establish a robust, flexible and responsive framework for corporate governance and consistent service delivery across some 700 business operating procedures.
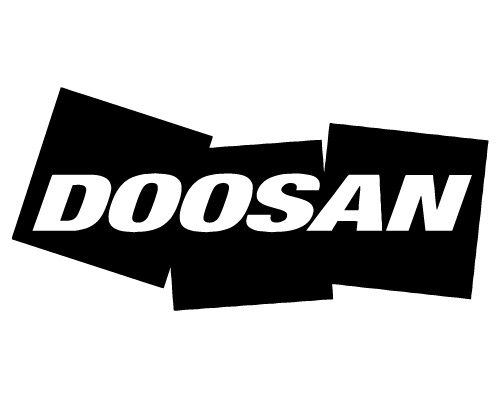
Our Isoma software simplifies continuous improvement across an entire organisation. What makes Isoma different? It’s built to engage and energise the workforce, not just automate it.
Solution
Doosan employed E-Squared to create an effective operating system for process management.
In order to test and control its use, Doosan chose to pilot this on its Outage Management Process (OMP): that which it uses to manage all power station refurbishment and environmental improvement work, including the installation of its leading clean combustion technology. The OMP project was rolled out in two clear phases across all UK operations.
Clarify and communicate
Phase 1 was aimed at clarifying, standardising and clearly communicating the detailed tasks which comprised the OMP to all the employees that were required to use it.
Improve delivery management
Phase 2 was aimed at improving the management of its delivery: ensuring its consistent application and measuring the regional or branch performance of its actual use. The company sought to create a complete, ‘live’, auditing system which enabled line managers, quality managers, senior managers and customers to track the compliant performance of ongoing outage work against consistent quality criteria laid out in Phase 1 and time criteria drawn from each customer contract. In Lean terms, its aim was to provide instant feedback against the Plan/Do/Check/Act cycle.
Implementation
The roll out against a challenging timescale was driven by the setting of a specific performance target against which all operational teams were managed.
Together these measures were critical to the project’s success: they ensured that the whole of Doosan Power Systems UK was engaged in its completion. From the outset, the project had clear ownership. The high-level vision created by the Deputy Managing Director for Services became a tactical project plan, owned by the Group QHSE Director and supported by the rest of Group QHSE management. Initially a project lead was created which developed into a full-time management role: powered and funded by the clearly-identified quality improvements and cost savings that the project could make.
The requirement for a framework that was robust, flexible and responsive to change, posed a complex array of challenges to Doosan.
- The business required a fully auditable continuous process improvement mechanism.
- Processes needed to be rapidly, effectively and consistently captured in order to deliver multiple, safe and replicable projects along with improved project returns.
- In order prevent process rework and reinvention, the company needed to capture additional information: specifically deep tacit corporate knowledge and individual ‘know how’.
- This information then needed to be made accessible to business and project delivery teams from a centralised intranet location.
- In order to eliminate the potential risk of introducing poor working practices within an environment of rapid business growth, new staff needed to be brought into the business and consistently trained in corporate standards.
We were able to meet these requirements since the E‑Squared software:
- Enabled very rapid and detailed identification of the OMP process at every level – critical due the scale of the task and the very challenging timescales for delivery;
- Gave users direct and centralised access to all of the information they needed to successfully deliver multiple, safe and replicable customer projects;
- Provided senior management with a clear, at-a-glance view of the progress by any branch or division on any contract at any time;
- Provided line management with the indicators they required to successfully manage each project;
- Was simple to install and operate: no manual feedback was required and the task of undertaking process and project audits was significantly eased.
Results
The result is that the creation of the OMP Reporting System has set an exciting precedent for Doosan.
The system has engaged the entire workforce in a much more interactive way of working and has enabled a new, dynamic way of managing both processes and major project delivery. Senior managers appreciate the direct feedback the system has created and site management see how key tasks and responsibilities can be much more easily identified and managed.
01
Impactful rollout
With the roll out of the system on the company’s Hunterston Power Station OMP project, its detailed financial impact on a specific customer project will shortly be assessable and the company has already started a wider roll out of the system beyond UK OMP. A parallel system is being created for the Construction Management Process (CMP) and both OMP and CMP are expected to be rolled out overseas, covering the company’s entire thermal, nuclear and pharmaceutical operations.
02
Innovative management
Beyond that it is hoped that the system will help Doosan manage the delivery of its innovative low emission power technology such as its Oxy Coal process which is helping the company consolidate its position as a global leader in carbon capture. Already tested on a full size a full-size 40MWth burner, the system captures in excess of 90% of the CO2 produced from burning coal.